Evolution of hot glue machine within the packaging industry
Dispensing hot melt adhesive for case and carton sealing is not new in the packaging industry. But for years the industry had seen little innovation in hot melt systems with the only option being a tank based system.
That is until recently when there has been a rise of new technology within flexible packaging equipment. First a true tankless adhesive system was released in 2013, with tank-free options quickly following.
What differentiates a system with a tank vs. one that is tank-free?
When looking at the different technologies you can immediately see a difference in the design and size of the melter.
Tank : The largest reservoir where adhesives are heated to a high temperature and remain at that temperature until dispensed. The size of the tank varies according to the system, but is generally 4 to 10 litres with the ability to go even larger than that.
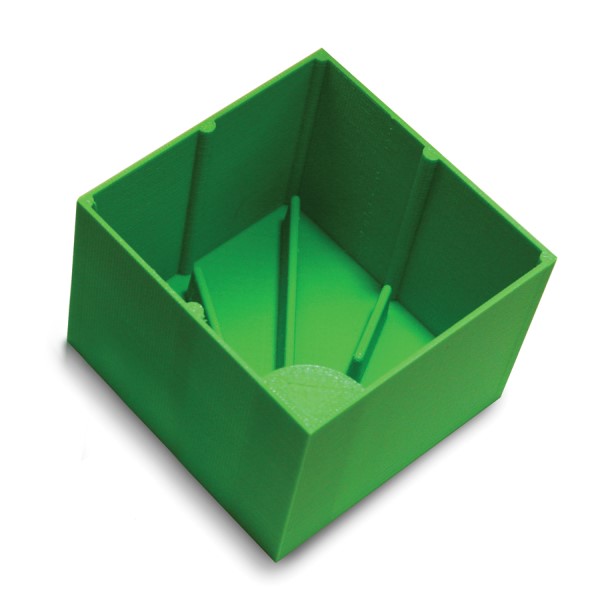
Tank-less: A smaller reservoir than for a tank-based system but it repeats the process of heating the adhesive to, and remaining at, a high temperature before it is used dispenses
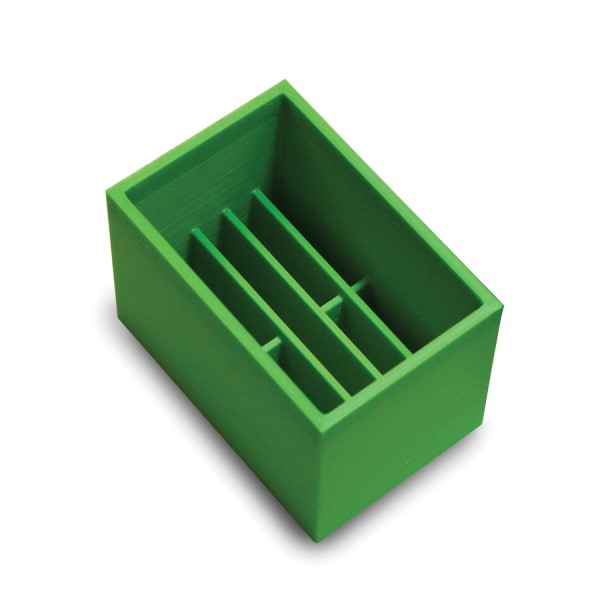
Tank-free: The InvisiPac Hot Melt System has no reservoir and, unlike tank systems, does not hold adhesive at a high temperature. It uses automatic feeding which adds adhesive when it is needed, so that adhesive is melted and dispensed on demand.
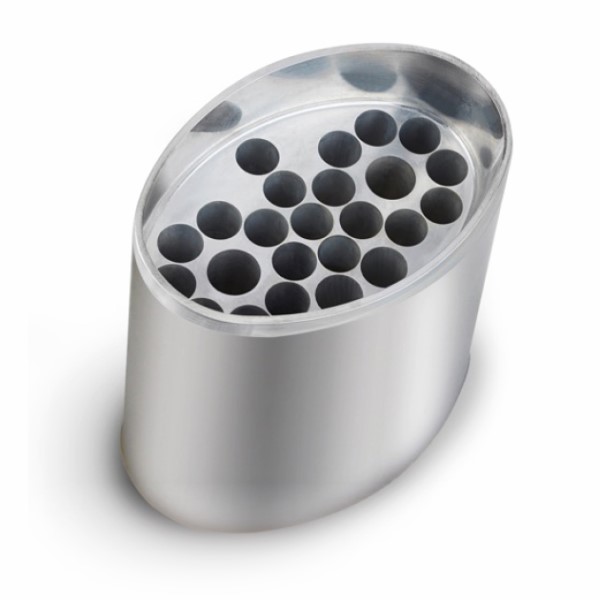
The fact that tankless adhesive dispensing equipment does not have a tank, produces major advantages in the processes, mainly in:
- a faster start-up time (10 minutes)
- improved adhesive quality
- decreased maintenance costs
Start-up time:
The biggest impact on the start-up time is the size of the tank/melting chamber and its melting surface.
If the melting surface of your reservoir is small compared to the volume of the reservoir, it will take much longer to heat up. This is definitely the case for tank or tank-less systems where the only melting surface they have are the walls. This is quite small compared to the volume inside.
The InvisiPac system, on the other hand, heats the complete melter which means that it has a 70% larger melting surface than comparable tank based systems.
When you compare the start-up times of each option, you can see a big difference in time:
Tank (4 to 10l):
45-90
minutes
Tank-less (1 to 5l):
30-40
minutes
Tank-free:
10
minutes
Improved adhesive quality
The high surface area to volume ratio and “first in, first out” technology of the InvisiPac tank-free hot melt system is designed to avoid adhesive degradation. It is important to know how the quality of the adhesive can be affected by the presence of a tank in the hot melt system. Some of the most common issues seen with tank and tankless adhesive systems are charring and thermal shock of the adhesive.
Charring: Adhesive that has been exposed to overheating, contamination, or oxidation and forms a burnt residue in the system. Overtime this charring can cause things such as blockages in the hoses, clogged applicators, and glue degradation. For more information on the causes of charring
Thermal shock: The result when lower temperature adhesives are added to, in large amounts, to high temperature adhesives. This changes the viscosity of the adhesive being used and impacts the quality of the seal, thus increasing the amount of adhesive used during packaging production
Decreased maintenance costs
With tank and tank-less systems, because the adhesives are heated to high temperatures and are kept sitting for a longer amount of time, a lot of time consuming issues can arise for maintenance professionals.
With the InvisiPac's tank-free design having melt-on-demand technology, there is a continuous flow of adhesive resulting in less downtime of the manufacturing process.
Tank/tank-less system | InvisiPac tank-free melter |
---|---|
Slowly heats up to its operating temperature (up to 45 minutes) | Reaches its operating temperature in less than 10 minutes |
Large quantities of adhesive kept at high temperatures for a long time | “First in, first out” melting provides continuous flow of adhesive |
Degrades adhesive integrity | The melt-on-demand process maintains adhesive integrity |
Creates adhesive char which causes plugged nozzles | Eliminates plugged nozzles and adhesive char |
Causes thermal shock (temperature fluctuations) when refilling adhesive | Removes operator exposure to burn hazards |
Exposes operators to burn hazards | Built-in adhesive tracking technology |
Related articles
Improve hot melt system performance
Improve the overall profitability of your packaging line by understanding the high price of outdated processes.
How to reduce the maintenance costs of your packaging line
Discover the benefits of switching from a tank-based system to a tank-free system
How to reduce cleaning of your hot melt system
A tank-free system like InvisiPac reduces the cleaning time and expense of your hot melt system.